The cornerstones of the Rudolph Logistics System
The Rudolph Logistics System (RLS) is based on the Fraunhofer Lean Logistics System and is firmly anchored throughout the entire company. Our Lean Management systems rests on four cornerstones that are put into effect in all areas of our business – always with the focus on supporting your business success just like ours.
Our logistics services are delivered by people. Our employees are the foundation of the Rudolph Logistics System. They are at once the creative basis and the strongest force for implementing improvements in the company. Their communication and continual striving to become better are what connect all the elements of the RLS together.
These are the four cornerstones of the Rudolph Logistics System:
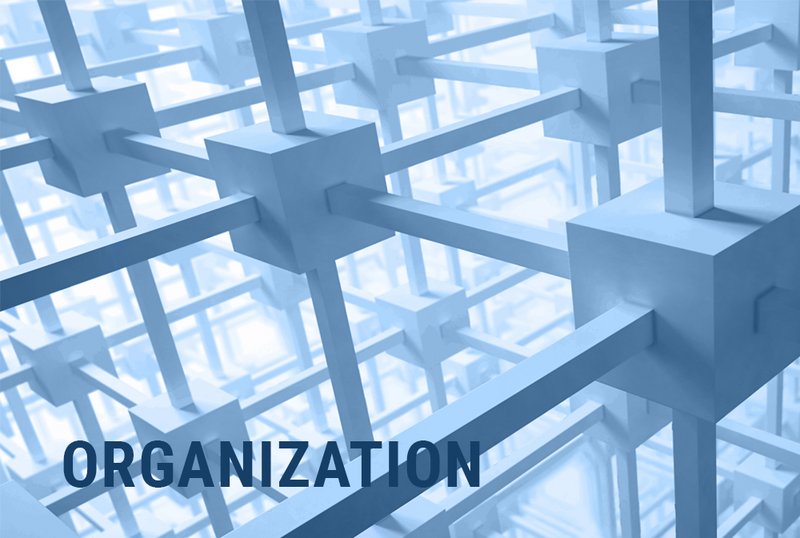
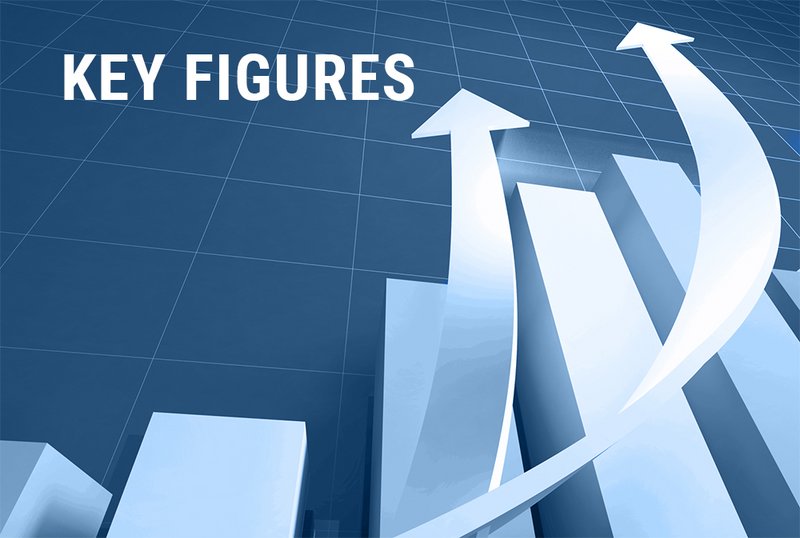
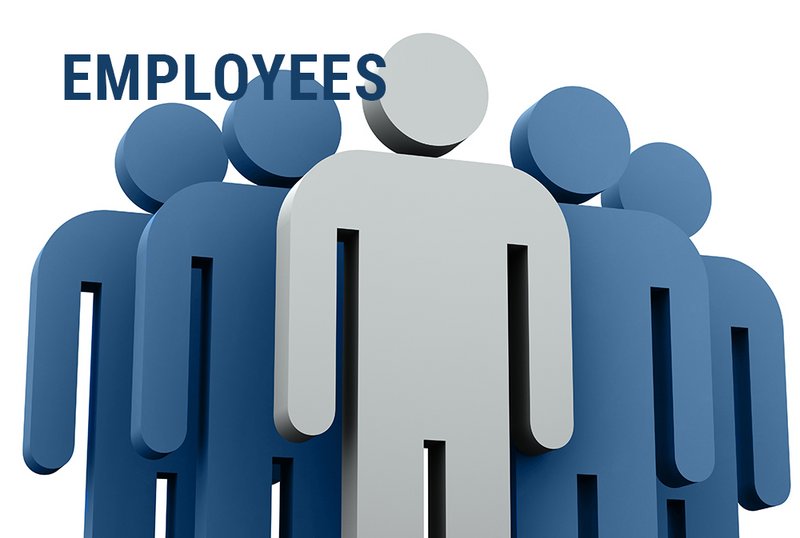
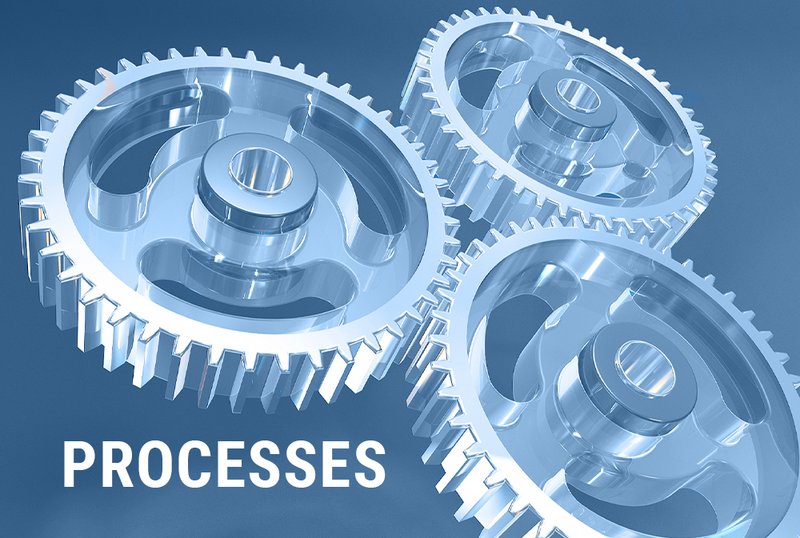
We have created an organizational framework that establishes Lean Management in our company and fills these principles with life. This organisation makes it possible for us to work on improvements – continually, in a structured manner, and with clear objectives in view.
To successfully reach targets, the Rudolph Logistics System works with clear and easy to understand key performance indicators. These indicators make changes visible for customers and employees.
The Rudolph Logistics Idea Management system provides important motivation for discovering potential improvements and making progress in these areas. This only works when all employees pull together. We encourage and support one another so that we can all live up to the requirements of Lean Management.
The processes that we provide to our customers are the central focus of all of the improvement measures that we undertake. But we don't ignore what's going on inside our own company. The administrative and support processes within our own four walls are also continually examined and developed further.
We establish clear conditions for lean logistics.
We have a clear organizational structure across all business fields and at all locations. From top management down to the level of operations manager there is a uniform structure throughout the group. At the operative level, on the other hand, we structure things according to the services that we are providing to our customers.
This gives you the advantages of having a dependable basic structure with customized arrangements that fit exactly to the specific demands of your logistics requirements.
A key factor in providing clarity for our organizational structures is that each of our employees has an exact understanding of his or her responsibilities. Job functions are clearly regulated and documented with transparency. This way you deal with the right contact person with the right skills in the right position.
Taken together this provides you with decision-making that is efficient and direct and competent contact persons to get the job done.
We define clearly understood and meaningful indicators as standards and guideposts for our activities.
In accordance with the motto "You can't improve what you haven't measured", we direct our activities on the basis of meaningful and easily understood key performance indicators (KPIs). We use KPIs that show the actual quality and productivity of our business processes.
But a number alone is not enough for us. In connection with continual improvement processes and shop floor management, we analyze each result and work on eliminating potential sources of error.
We visualize the current status of the KPIs for each location so that they can be seen by all employees. In this way we make it possible for each employee to have a clear view of the performance of his or her team.
The various quality KPIs that we work with give a clear answer to the question of how well your requirements are being fulfilled.
We support and encourage one another and expand our skills to meet company goals.
Our employees are the living embodiment of the Rudolph Logistics System. They are the ones who advance the ongoing improvement process and thus continually improve the services that we provide to our customers.
Personnel development is very important to us. We want to give our employees all of the skills they need to do their jobs with excellence and high motivation. Training programs and workshops as well as onboarding programs for (new) employees are designed to provide these skills. We document these measures using a qualification matrix.
Combined with a healthy amount of personal initiative that we expect from employees, this yields a system where stable, successful processes and innovative ideas can flourish.
For you that means being sure that your processes are in the best of hands.
We design lean processes and improve them continuously.
We are convinced that each and every process can always be improved. This basic idea motivates our employees to always be thinking about possible improvements in daily activities and to be ready to examine themselves and their work.
All processes are transparently and uniformly documented. Each process step is clearly assigned to a process owner. The process owner is responsible for managing and tracking the specified productivity and quality KPIs.
For process optimization we make use of highly practical and pragmatic methods and tools – always with the intention of undertaking improvements methodically and in a structured manner.
For you that means clear information about what we want to accomplish for you.